Egg Grading Machine Manufacturer Moba Rebuilds iMoba Platform
Moba, the world’s largest manufacturer of egg grading machines, wants to continue to grow and is fully committed to digitalization. There are now 300 egg-grading machines connected to the iMoba platform, but Moba is aiming for 1,500 connected devices. Together with Info Support, the manufacturer rebuilt the architecture of the iMoba platform. The result is a modern data platform.
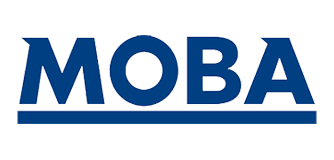
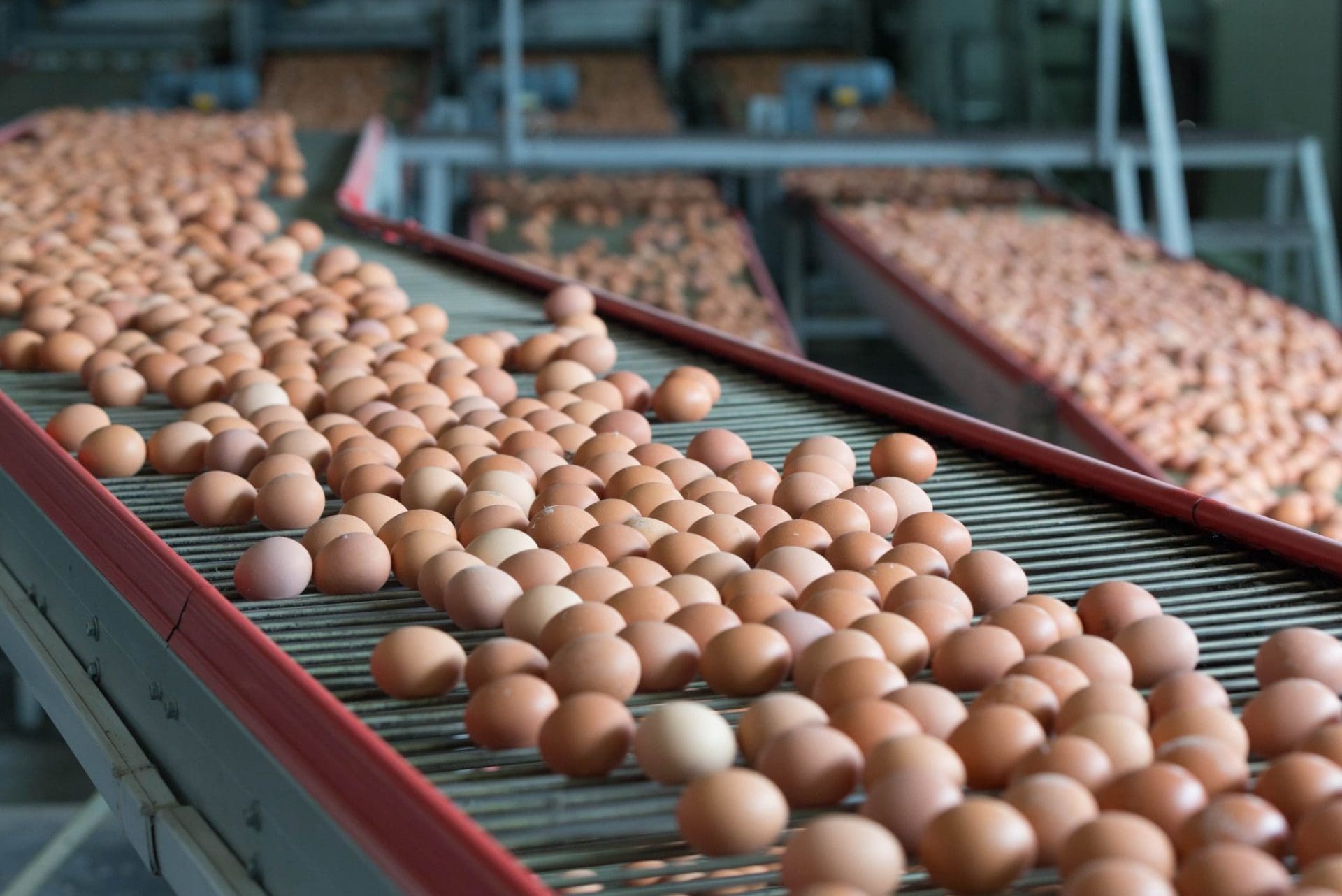
Challenge
A data platform that is not already dated in five years and preventing costs from growing proportionately as more machines are connected.
Target Audience
Users of egg grading machines.
Result
A modern dataplatform.
Rebuild platform for better scalability, insight and cloud cost control
Moba faced quite a challenge. Having growth ambitions is one thing, but Moba also wanted a data platform that would not already be dated in five years. In addition, the manufacturer wanted costs to remain manageable and had a specific desire in this regard. There are many more machines at customers worldwide than are digitally connected to the iMoba platform. Preventing costs from growing proportionally with the connection of more machines was an important goal.
The decision was made to rebuild the entire platform. The main arguments for this were better scalability, opportunities to give customers more insight, and cloud cost control. “With the rebuild of the iMoba platform based on Microsoft Azure, we have avoided costs rising disproportionately with the connection of more machines,” says Rick Oonk, project manager from Info Support. “In addition, we now handle data smarter. The moment you connect a machine, the raw data is first stored. Then the machine sends the data to the platform.”
Clear picture of what happens in the egg production line
With the data now being collected, Moba and its customers have more insight. Oonk: “The physical world is increasingly closer to the digital world. As a company, you can and should give customers insight into how the machines work. For example, about how many eggs go through per hour. Sensors also see if there is a crack or blood on the eggs. That data gives Moba and its customers insight into how machines are performing. They see why there are differences and what could be improved. In turn, the actual users of the machines also see how their machines are performing. For example, there is insight into how many eggs of what size are being processed. This data goes directly into the cloud, creating a clear picture of what is happening in the egg production line,” says Oonk.
Bringing the physical world and IT together is what Info Support does best.Rick Oonk, Project Manager at Info Support
Understanding the entire chain
The rebuilt platform helps Moba provide customers with even better services. The data is well secured and only accessible by the owner. It also collects anonymized data from which hugely valuable insights can be distilled, offering two possibilities. First, end users can benchmark themselves against this anonymous data and thereby gain quick insight into which areas they can still improve. Second, developers within Moba can draw guidance for future developments from the insights.
Oonk: “Power BI dashboards give the company more insight. In addition, it can have KPIs monitored for service engineers. In addition, the cloud architecture we developed offers the ability to create visualizations (digital twin) and dashboards and to run reports on this data.” Oonk continues: “This gives Moba insight into all kinds of cross-sections of data relevant to various departments. These give the company insight into the entire chain, from ground to mouth. The amount of data Moba has at its disposal is really very valuable to the company.” Paul Buisman, Director Innovation at Moba, adds, “The extra flexibility and insight into what machines consume in terms of data are very welcome. As Moba Group, we want to remain the biggest. That is only possible if you have and keep a grip on what is happening in your own chain.”
Store data smarter to cut cloud costs in half
Info Support also supported Moba in cutting cloud costs in half. This was achieved, in part, by storing data more intelligently. Oonk: “There is a lot of data available, but customers do not request all of it. We therefore made a split between current data, for which you want to be able to request information at the egg level, and data older than three days, for which only trend analyses are relevant.”
Moba customers can access all data via their own dashboard at any time. Data older than three days is accessed less frequently and has been moved to a place where storage is a lot cheaper. Of course, this data can still be called up for annual reports or reports, for example.
Making an impact on the value chain
The project was successfully completed. “It was a far-reaching project, from construction to testing. You perform a rebuild, but in doing so you actually copy all the data first and then process it in other systems with different requirements. After all, the goal is to achieve improvement,” Oonk says.
What Oonk also emphasizes is that a whole value chain precedes the moment eggs are in the supermarket. “What I think is cool about this kind of project is that as a consumer you are totally unconcerned with how the eggs get to the supermarket. Eggs are not only tracked, but graders also check the quality of the eggs. That means checks for blood, dirt, size and any cracks. You don’t realize that when you stand in the supermarket as a consumer.” Oonk continues: “We are really adding value in the chain with the iMoba platform. Moreover, the project was carried out by the world market leader. Thirty percent of all eggs worldwide pass through a Moba grader. And the eggs that are physically visible in the machine are now processed digitally in a modern cloud application.